Continuous improvement: principles, methods and processes to be implemented

A company is constantly forced to move forward, to progress. To stagnate is to regress. With a view to perpetual innovation, the implementation of continuous improvement has become vital. There are many tools that can be used to achieve these new objectives, without making major upheavals all at once. It is about making small changes by applying methods that have already been proven in sustainable industries, because improvement must be synonymous with progress.
Continuous improvement process: what is it?
The process of continuous improvement is an ongoing effort to improve the business. These efforts can be aimed at making small improvements at regular intervals or, on the contrary, at consolidating all the improvements into a global implementation.
When a company engages in continuous improvement, it aims to gradually increase quality, customer satisfaction, and therefore profits. Improvements are made to services, products and processes with the aim of reducing costs, lead times, inventory and waste.
Feedback comes from employees and customers themselves. Teams are involved in the stages of change. In this sense, a reward system for ideas for progress can make sense.
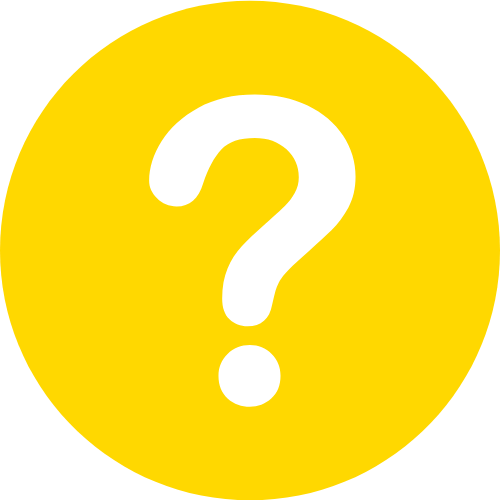
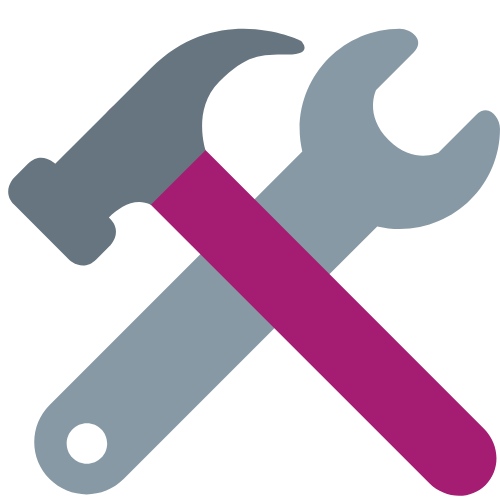
What are the tools for continuous improvement?
There are many tools and methods for implementing continuous improvement. These include Kaizen, Lean Management, Six Sigma and Kanban. All are principles for increasing productivity. Continuous improvement tools are used to solve problems in production, waste or process efficiency.
Many of these tools originated in automotive factories and other industries, where speed and just-in-time production are the norm. In order to increase productivity and quality of work, the methods are applied to all processes in the company, from management to workers, from administrative departments to production lines.
Lean management
Applying Lean management to continuous improvement means seeing every problem as an opportunity for improvement, keeping employees at the heart of the action as each person sees their own workstation as an area for improvement. The idea here is that every problem to be solved is a learning experience that is fully integrated into the company’s culture.
The implementation of Lean is based on these methods:
- challenge what is currently being done;
- explain how to do it, not why you can’t do it;
- consider employees and observe their workstations;
- accept to move slowly and in small steps;
- minimise the costs of solutions;
- keep asking “why?” and find the root cause;
- organise regular meetings to update new ideas.
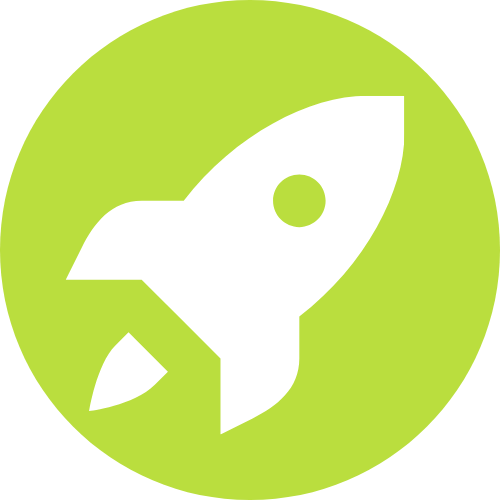
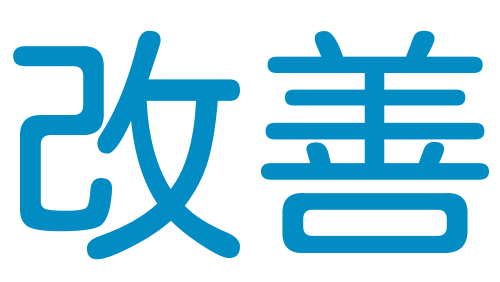
The Kaizen method
In the context of implementing step-by-step changes, we find the Kaizen method applied to continuous improvement. This is its literal translation from the Japanese Kai (“change”) and Zen (“good, better”). This method was born in Toyota factories in the 1950s. It consists of introducing small changes that will eventually lead to big advances.
It is a gentle method that follows the principles of Lean. Here, we do not blame, we seek to understand and do better.
The Kaizen method can be summarised as follows:
- challenge themselves;
- prioritize changes ;
- correct errors immediately;
- be proactive;
- seek stability ;
- eliminate waste ;
- take into account the opinion of the teams.
PDCA (Plan Do Check Act) and the Deming wheel
PDCA stands for Plan-Do-Check-React. This method is used in the quality approach to business processes and is also known as the PDCA Deming Wheel, after its creator W. Edwards Deming. It establishes a cycle of problems and then improvement processes.
Plan
- identify problems ;
- define the objectives to be achieved ;
- define the resources available or to be acquired ;
- to interest the teams in the project;
- establishing a schedule, processes, estimating costs;
- set up performance indicators.
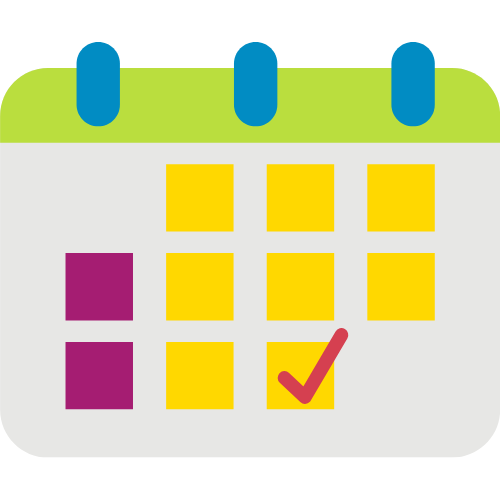
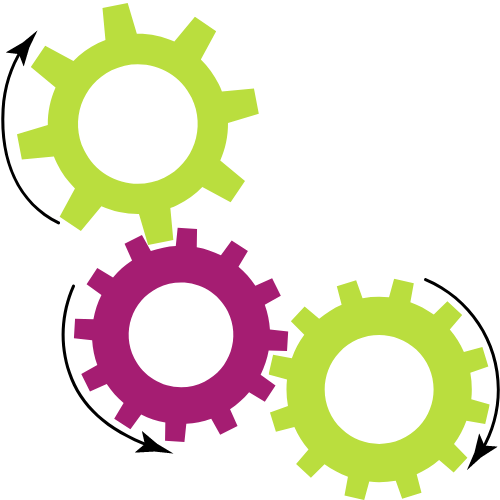
Do
Action must be taken through the teams and management. This phase is dedicated to the deployment of solutions, according to the modalities decided during the planning stage.
This implementation can be carried out by the people concerned or entrusted to a third party, provided that the task is well defined.
Check
This involves measuring the results obtained following the deployment of actions. These are compared with the objectives and correlated with any corrective action.
After a certain period of time defined beforehand, the measurement of the KPIs makes it possible to judge the effectiveness of the approach in a totally objective manner. If the expected results of an action are not achieved, you can then make adjustments.
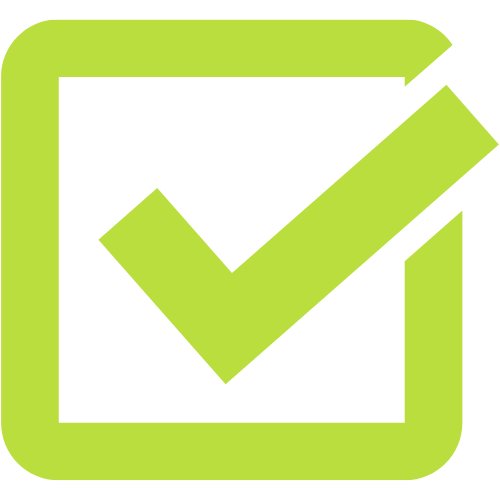
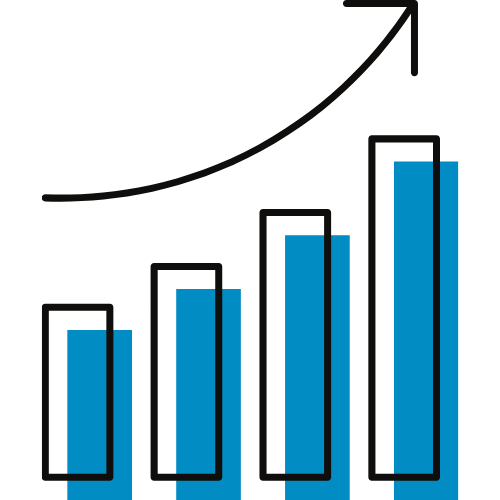
Act
The effectiveness of the actions implemented is checked. If the results do not correspond to the objectives, management may decide to start a new cycle with the same objectives, or revise them upwards or downwards, after having defined new levers for action.
A tool to implement
a continuous improvement process?
Lean office: continuous improvement applied to administrative processes
Lean office is part of the continuous improvement process. It is particularly relevant to employees, as it deals with the processing of information rather than the physical flow of production.
Borrowed from industrial optimisation techniques, the objective of the Lean Office is to maximise the performance of administrative processes and service activities.
Waste, lack of interaction between departments, lack of communication, lack of objectives and lack of a company policy will be eliminated. Implementing tools such as PDCA or Kaizen makes it possible to obtain performance indicators. When applied to service activities, these methods give very good results.
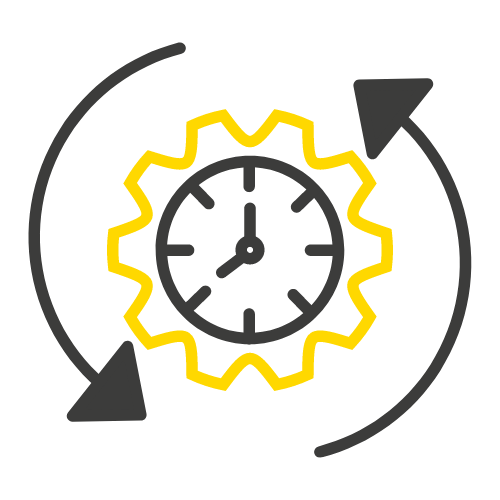
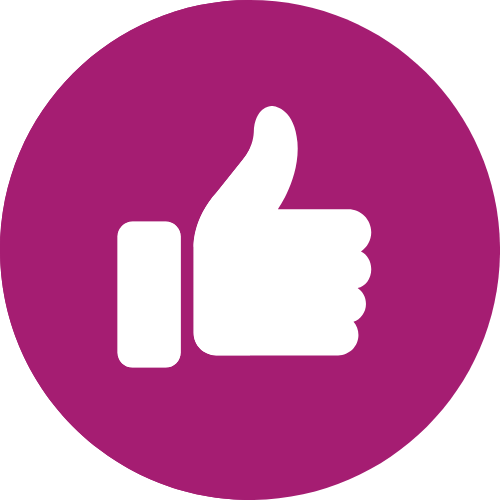
Good practices for deploying a continuous improvement process in your organisation
Engaging the company in a process of continuous improvement means that it gains in quality and profit, directly induced by the customer satisfaction that results from the methods developed.
You will also have understood that the teams remain at the centre of the improvements in order to carry out the different stages. Applying soft methods of organisation allows employees to be involved in order to get the best out of them.
Here are some examples of good practices for efficient continuous improvement:
- putting teams at the heart of change processes;
- identify problems ;
- implement corrective actions;
- deploy the methods described earlier in this article;
- keep customer satisfaction in focus.
Conclusion
In order for a company to keep moving forward and progressing, the implementation of a real continuous improvement approach is necessary and strategic. Different methods and tools can be used to optimise processes and gain in efficiency.