La plupart des entreprises souhaitent s’inscrire dans une démarche d’amélioration continue qui leur permettra de poursuivre leur croissance tout en limitant les coûts, afin de mieux résister à leurs concurrents. Une telle stratégie nécessite une multitude de transformations à différents niveaux (direction, équipes, comportements individuels, etc.). Elle s’appuie également sur une démarche nommée l’excellence opérationnelle. Voici quelques précisions qui pourront vous être utiles sur ce sujet.
Qu’est-ce que cette notion ?
Vous serez peut-être surpris d’apprendre qu’il n’existe pas une définition officielle de l’excellence opérationnelle. Dans la pratique, et quels que soient les secteurs d’activité, cette notion est associée à la capacité de mettre en œuvre des principes et des processus permettant une production conforme aux attentes des clients avec une rentabilité maximale. Elle regroupe également différentes méthodes ayant pour but la recherche de la meilleure productivité possible.
Elle s’apparente donc à un véritable levier de croissance pour les entreprises. Elle dope la production, tout en réduisant les risques opérationnels potentiels. Pour évaluer toute la pertinence de sa mise en œuvre, il existe à ce jour plusieurs dispositifs tels que le modèle EFQM, le six sigma ou encore le « lean management », pour ne citer que les plus connus.
Cette démarche doit être partagée par tous les acteurs de l’entreprise, en vue d’en donner sa pleine mesure. Elle pourra ainsi faire partie intégrante de la philosophie interne. L’excellence opérationnelle s’appuie sur des processus solides dont la qualité n’est certainement plus à démontrer. Certains peuvent être qualifiés de fondamentaux et nécessitent la définition d’un plan d’action pour maximiser leur efficacité naturelle. Trois d’entre eux seront détaillés au cours des paragraphes qui suivent.
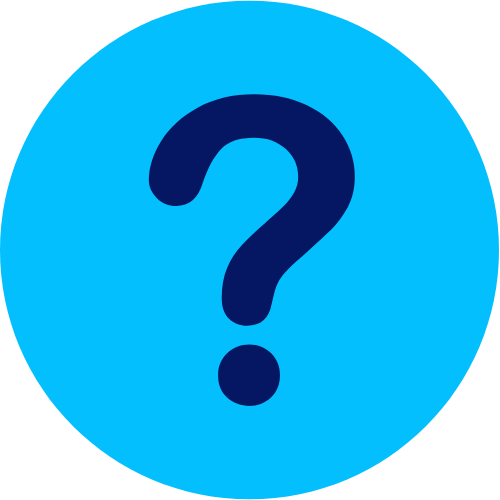
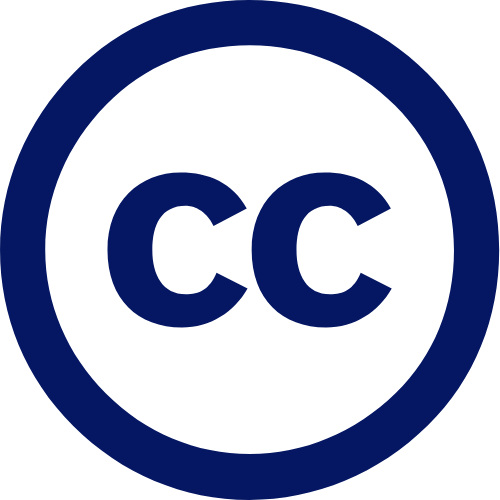
Gérez les standards de travail
Au sein d’un environnement industriel, la documentation des principes de fabrication ou des circuits de prise de décision est essentielle. Chaque standard de travail doit également être documenté. En effet, il est précieux que chaque tâche effectuée par les opérateurs soit décrite (ainsi que toutes les phases qui la constituent), notamment celles qui vont avoir un impact direct sur la réduction des risques affectant la productivité globale des équipes et de la société (retard de fabrication, produits non conformes, gaspillages divers, etc.).
De telles informations doivent aussi être mises à jour en fonction de l’évolution des produits, des méthodologies de travail, des ressources disponibles pour les fabriquer et des évolutions du système ou de la technologie présente dans l’environnement professionnel. Sans cette veille, les standards perdront rapidement leur efficacité au fil du temps. La digitalisation de ces documents permet de faire face à ce défi. Elle participe également à une meilleure diffusion des informations auprès des différents acteurs. Le management des standards de travail peut également être assimilé à l’une des étapes du « lean management ».
Un outil pour atteindre
l’excellence opérationnelle au travail ?
Les méthodes A3
Elles doivent leur nom au célèbre format de papier équivalent au double d’une feuille A4. Le système A3 regroupe les méthodes visant à résoudre les problèmes. Il repose essentiellement sur la décomposition des difficultés et son fonctionnement s’articule autour de six étapes :
- Il faut d’abord commencer par identifier clairement le problème ainsi que toutes ses composantes (origines, conséquences sur les secteurs d’activité, etc.).
- Dans un second temps, il est primordial de faire un état des lieux précis et définir les objectifs à atteindre.
- Il s’agit ensuite de concentrer votre attention sur les causes du problème actuel. Analysez-les précisément afin de comprendre leurs impacts réels.
- Il est alors possible de résoudre la difficulté. Identifiez au moins cinq solutions potentielles. Effectuez ensuite un classement en fonction de l’importance de leurs impacts.
- Un plan d’action pour la mise en application des décisions que vous aurez choisies peut être défini. Efforcez-vous d’être dès à présent le plus précis possible.
- La dernière phase de ce processus consiste à effectuer le suivi des actions correctives. Ont-elles les effets escomptés sur la problématique en question ou est-il nécessaire de les ajuster ?
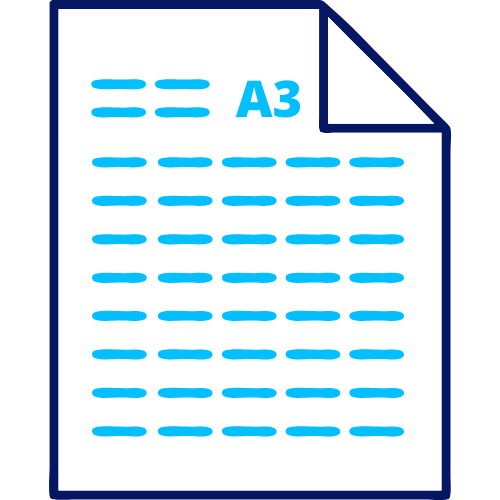
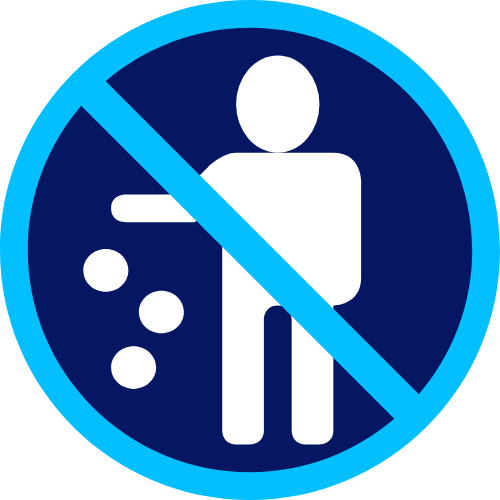
Réduire les gaspillages
L’excellence opérationnelle passe également par la réduction (voire l’élimination pure et simple) des gaspillages générés par la production et de ce fait de réduire les coûts. Ces gaspillages sont de différentes natures. Sept grandes familles peuvent être distinguées :
- Le surstockage : désigne les stocks « dormants » ou « morts ». Cet élément est révélateur d’un dysfonctionnement dans l’équilibre de la gestion des approvisionnements, de la production des produits finis et de leur livraison.
- La surproduction : comme son nom le laisse à penser, il s’agit d’une production de pièces supérieure aux quantités réellement commandées. Ce phénomène conduira presque inévitablement au surstockage.
- Les transports inutiles : ils sont fréquents sur les sites disposant de plusieurs lieux de stockage. Des déplacements de matières premières sont alors souvent nécessaires, se traduisant par des consommations inutiles de temps, de ressources et de technologies.
- Les déplacements inutiles : on se concentre avant tout sur le poste de travail. Si l’espace est mal organisé ou peu ergonomique, le personnel est alors obligé de se déplacer, ce qui occasionne des pertes de temps et augmente le risque d’un accident professionnel.
- Le surprocess : il s’agit typiquement de toutes les tâches sans la moindre valeur ajoutée réelle.
- Les temps d’attente entre deux tâches : ils doivent être réduits au minimum.
- La fabrication de pièces non conformes : elle affecte directement la rentabilité et la réputation de l’entreprise. Les taux de rebut doivent, eux aussi, être les plus faibles possible.